9th International Workshop on Numerical Modelling of High Temperature Superconductors - HTS 2024
Parkhotel Bad Zurzach, Switzerland
Thank you for attending the HTS 2024 workshop
W E L C O M E
The research and development of modelling tools and approaches is a fundamental subject in applied superconductivity.
High Temperature Superconducting (HTS) materials raise complex challenges in the design and prediction of devices behavior due to their thermal and electromagnetic dependencies and non-linearities, hysteresis, anisotropy, high wire aspect ratio and interaction with other functional materials.
For this 9th edition, the topics of the workshop are organized into three main categories:
Innovative methods and tools for modelling large-scale HTS systems
- Improvements in fundamental numerical methods to simulate superconducting materials, including HTS, MgB2 and iron-based materials.
- Innovative methods and tools for design and simulation of HTS materials.
- Original, novel application of commercial numerical software packages,
- Open access modelling and simulation resources for teaching, training and research.
Coupled & uncoupled multiphysics problems
- Computation of AC losses under distinct regimes.
- Thermal modelling (coupled and uncoupled).
- Mechanical modelling (coupled and uncoupled).
Applications in large instruments such as high-field magnets, medical magnets and accelerator magnets
- Design and optimization tools for HTS devices for power/transportation applications [Topics include energy storage, including SMES and flywheels; fault current limiters; power cables; transformers; wind generators; stacked tape machines; and others],
- Development of tools for integration with power grid software simulators,
- Novel applications of HTS materials.
The HTS Modelling Workshop aims to bring together researchers specializing in physics, mathematics, and electrical engineering applied to new and existing computational methods, the development of modeling tools, the advanced use of simulation software and the design of superconductivity applications in the industrial environment.
The workshop format facilitates discussion among researchers, which is necessary to achieve their objectives.
The HTS 2024 Modelling Workshop is hosted by
The HTS 2024 Modelling Worshop is sponsored by
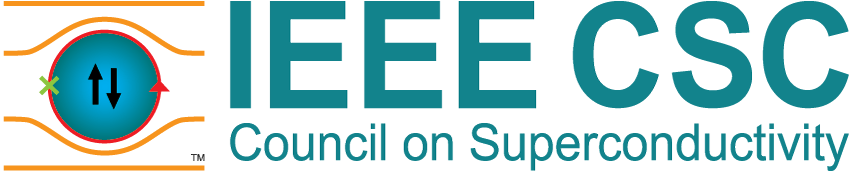.png)
-
-
18:00
Welcome Apero and Workshop Registration
-
18:00
-
-
1
Workshop Registration
-
2
Workshop IntroductionSpeaker: Stephane Sanfilippo (PSI - Paul Scherrer Institut)
-
Session 1: Coupled & Uncoupled Multiphysics Problems: A
-
3
Numerical Considerations for Coupled Magneto-thermal FE Models of HTS Tapes
The accurate prediction of AC losses in High- Temperature Superconducting (HTS) tapes has been widely discussed in the literature, as both homogenized and multi-scale models have been proposed using different magnetodynamic finite-element (FE) formulations. In this work, we discuss numerical considerations to be taken into account when coupling magnetic and thermal FE models. The validity of using homogenized models, the accuracy of the time-stepping procedure and the difference between monolithic and staggered coupling schemes are discussed. These considerations are illustrated for a 2D model of a racetrack coil made of several REBCO tapes, both during normal operation (no quench) and in thermal runaway.
Speaker: Louis Denis (University of Liege) -
4
Voltage signals on terminations of an HTS magnet modelled in T-A formulation
In this contribution is demonstrated how to evaluate in T-A formulation the “macroscopic” voltage in turns of HTS magnet energized by AC current. Decomposing the local electric field into the vector-potential induced and the electrostatic-charges initiated part allows to integrate the latter along the whole length of conductor, and compute in this way the voltage signal that will appear at the magnet terminations. On top of serving for checking the correctness of numerical computation, this quantity can be directly measured in experimental testing. As an example is shown the expected voltage signal on terminations of a pancake coil wound from coated conductor tape.
Speaker: Fedor Gömöry (Institute of Electrical Engineering, Slovak Academy of Sciences)
-
3
-
09:45
Coffee Break
-
Session 1: Coupled & Uncoupled Multiphysics Problems: B
-
5
Modelling the behavior of HTS coils under overcurrent conditions
To improve the understanding of High-Temperature Superconducting (HTS) devices in electrical systems, it's important to couple Finite Element Models (FEM) with Electrical Circuits (EC). This coupling should consider superconducting behavior and how HTS devices affect electrical systems. Some HTS devices shift from the superconducting state to the normal resistive state, like fault current limiters, which requires modelling dynamic state changes. This transition leads to modelling challenges due to the current redistribution among the superconductor and the surrounding conductive materials. In this study, a Multiphysics FEM coupled with an EC was developed to address specific challenges of 2G HTS coil overcurrent operations. In addition, this study presents methods for reducing the Electrical Circuit Model (ECM), significantly reducing computational costs by a factor of 6 while maintaining a remarkable agreement with experimental results and full models.
Speaker: Gabriel Hajiri (Université de Lorraine - GREEN) -
6
3D thermal-hydraulic and electric modelling of quench propagation in HTS conductors for fusion
3D thermal-hydraulic and electric modelling of quench propagation in HTS conductors for fusion
Andrea Zappatore
Energy Department
Politecnico di Torino
Turin, Italy
andrea.zappatore@polito.itAbstract—A fully three-dimensional multi-physics model to simulate quench propagation in HTS conductors for fusion applications is presented. It accounts for thermal, electric and fluid dynamics throughout the entire transient. It gives a deeper insight into the evolution of relevant quantities, e.g., the temperature in the bulky structure of the conductor, with respect to the typical 1D models. A preliminary validation against experimental results show satisfactory agreement.
Keywords—3D, thermal-hydraulic, electric, quench, HTSINTRODUCTION
Quench propagation in high current conductors based on High Temperature Superconducting (HTS) material is an open issue due to the small normal zone propagation velocity. This makes the quench much more challenging to be detected than for conductors made of Low Temperature Superconducting (LTS) materials. For this reason, an extensive test campaign is ongoing within the EUROfusion Consortium in order to characterize experimentally different conductors design from the quench point of view. Also, this experimental campaign aims at building a database to calibrate and validate numerical models which can then be more reliably used for the simulation of quench in full conductors and/or on different designs.
Several conductors have already been tested [1] and more will be tested in 2024. A calibration and validation exercise has been successfully accomplished [2] modelling the quench propagation with a 1D code [3].
This modelling approach is based on lumping the cross-section of the solids and of the fluids in each axial nodes. This implies assigning a single value of temperature for the solids and of speed, velocity and temperature for the fluids.
However, this approach has some limitations, i.e., a limited capability in discretizing the cross-section of the conductor. This becomes important in the case of bulky structure as those foreseen in different designs of HTS conductors, see for example Figure 1. In order to provide a more detailed description of the three-dimensional distribution of relevant quantities, a fully 3D multi-physics model is presented here.Figure 1 CAD view of the non-twisted conductor tested in the quench experiment in SULTAN. The dark orange squares are the stack of REBCO tapes, the light orange round regions are the copper profiles in which the stacks are enclosed, the cyan region are the voids where helium flows and the grey conduit is the jacket which serves as helium containment and mechanical support to the cable.
3D MODEL
The 3D model accounts for an electric, a thermal and a fluid model, which are coupled together to follow the transient under analysis.
Electric model
The current density distribution in each cell of the domain is computed from Eq. (1) reported below.
∫_A▒〖1/ρ (∇ϕ)dA=0〗 (1)
where ϕ is the electric scalar potential, ρ is the electric conductivity and A is the cell face of a generic cell of the discretized domain.
The electric conductivity in the superconductor is given, according to the power law, as
ρ=E_C/(J_C (B,T)) (□(J/(J_C (B,T))))^(n-1) (2)
where EC = 100 μV/m, J is the current density and JC is the critical current density at the given magnetic field and temperature. The magnetic field is the background field of SULTAN, which has a peak value of 10.9 T in the High Field Zone (HFZ), which is much larger than the self-field, which is therefore neglected. The temperature is computed by the thermal model. The volumetric heat source is computed by the electric model according to the Ohm’s law as Q = J∙E.
The electric conductivity in the normal conducting region is temperature dependent and, in case of copper, it accounts also for the magnetic field and RRR.Thermal model
The thermal model solves the 3D transient heat conduction equation. This equation is coupled to the fluid temperature one (see next sub-section) as well as to the electric one, as the Joule heating becomes the heat source as soon as the quench is initiated.
All the thermophysical properties are temperature dependent and, in case of copper, the thermal conductivity depends also on the magnetic field and RRR.
The density and specific heat capacity of the stacks of tapes are homogenized according to the mass and heat capacity, respectively, based on the composition of the layer of the tapes and of the solder among them.Fluid model
The fluid model solves the full set of Navier-Stokes equations, computing the velocity, pressure and temperature of the helium in the voids where it flows, see Figure 1. The presence of turbulence is accounted for using a k-ω model for its closure. In order to cope with the strong non-linearities of the helium thermophysical properties, a coupled approach has been chosen as solver of the set of equations.
RESULTS
In this section, a preliminary validation against experimental data is reported. After that, the main results are briefly reported and discussed.
Preliminary validation against experimental data
In Figure 2(a), the comparison between the local temperature in the strand, in the helium flow and in the jacket show that the computed model is able to correctly follow the temperature increase in different locations of the conductor. Except for a small anticipation (roughly 2 s), the computed and measured temperatures agree, meaning that the model can be trusted to analyze more in detail the evolution of the transient.
This is also confirmed by the comparison of a local voltage measurement in the quenching region, see Figure 2(b).(a)
(b)
Figure 2 (a) Temperature evolution in the quenching region of the conductor. The measured and computed strand and jacket temperatures are compared. (b) Measured and computed voltage evolution in the quenching region.
Jacket temperature distributionIn Figure 3, the distribution of the temperature of the jacket is reported, showing a strong non-uniformity in the cross section. Also, in Figure 4, on the external side of the jacket, a variation of 30 K (when the peak temperature there is 90 K) is obtained. This set of results shows quantitatively the implication of having a point contact of the quenching strands with the jacket and the thick structure of the jacket itself. These two features lead to a non-uniform distribution in the azimuthal direction and the second implies a slow heat propagation in the steel cross section, leading eventually to a three-dimensional transient distribution.
This can impact the capability of reliably following the this transient in a quenching conductor with other, simpler model. Also, this much more detailed model can give insight on the behavior of alternative quench detection strategies, e.g., fiber optics, which are sensitive to the local temperature distribution.Figure 3 Computed temperature distribution on the external surface of the jacket and on its cross-section in the quenching region.
Figure 4 Azimuthal temperature distribution on the external surface of the jacket. A third of the external circumference is reported, corresponding to the red double arrow shown in the inset.
CONCLUSIONS AND PERSPECTIVE
A 3D thermal-hydraulic and electric model for the simulation of quench propagation in conductors for fusion applications has been presented. A preliminary validation shows it gives reliable results and the analysis of the quench evolution shows a fully 3D temperature distribution in the conduit of the cable. These results can help giving feedback to the design of alternative quench detection and to thermo-mechanical analysis, which are being implemented to understand the degradation mechanisms due to quench, which was experimentally observed in several conductors.REFERENCES
O. Dicuonzo et al., "Upgrade and Commissioning of the SULTAN Facility to Host Quench Experiments on HTS High Current Conductors," in IEEE Transactions on Applied Superconductivity, vol. 31, no. 5, pp. 1-5, Aug. 2021, Art no. 9500505
A. Zappatore et al., Quench experiments on sub-size HTS Cable-In-Conduit Conductors for fusion applications: Data analysis and model validation, Cryogenics, vol. 132, 2023, Art. no. 103695
A. Zappatore et al., A new model for the analysis of quench in HTS cable-in-conduit conductors based on the twisted-stacked-tape cable concept for fusion applications, Superconductor Science and Technology, vol. 33, 2020, Art. no. 065004.Speaker: Andrea Zappatore (Politecnico di Torino) -
7
Critical current numerical characterization of 6-layers CORC® cables
In perspective of 20 T+ field magnet and more compact layouts for fusion reactors, the high temperature superconductors are the alternative which can allow high transport current at very high field, guaranteeing at the same time a higher stability. Among them, the Rare-Earth Barium Copper Oxide (ReBCO ) coated conductors are a promising option due to their high critical temperature and the extremely high critical current density. The CORC® cable concept, based on ReBCO HTS tapes wound around a copper former, is of particular interest for these high-field magnet applications due to its round cross-section and electrical and mechanical isotropy. However, these cables can degrade as a result of the winding process and operating conditions. Thus, a comprehensive characterization of their performances is necessary. The complex geometry and shape of the CORC® cable makes tricky to numerically reproduce the correct current distribution among tapes, which strongly affect the cable behavior, especially co of number of layers (>3 layers). This work presents a 3D multi-physics numerical model for characterizing the critical current (Ic) of more complex CORC® cable layouts, based on a T-A formulation model in COMSOL Multiphysics coupled with a thermal model of a straight cable, already validated against experimental results. For the first time, a self-consistent boundary condition allowed the computation of the current distribution in a 6-layers CORC® (12-tapes total), aimed to the replication of the Ic. The tape is approximated as a thin shell, taking advantage of its high aspect ratio, and the Ic scaling for the tape accounts for the temperature, magnetic field and local strain due to the winding on the copper core. The assessment of the voltage-current curve for the conductor has been performed against experimental and numerical data present in literature.
Speaker: Sofia Viarengo (Politecnico di Torino, Turin, Italy) -
8
The role of ferromagnet to prevent the flux-jump occurrence: a numerical study
Although thermomagnetic instability can deteriorate its performances, MgB$_2$ has been proved to be one of the most promising superconductors for magnetic shielding. For this reason, finding solutions to reduce or prevent thermomagnetic instabilities is mandatory. A numerical approach can be a powerful tool for predicting the occurrence of such phenomena, thus facilitating the development of superconducting devices including magnetic shields. This study focuses on the numerical analysis of the effect of the addition of a ferromagnetic layer on the mitigation of flux jump occurrence in a MgB$_2$ cup-shaped shield subjected to axial magnetic fields.
Keywords: magnetic shielding, thermal instabilities, numerical modelling, bulk
superconductorSpeaker: Michela Fracasso (Politecnico di Torino) -
9
Impact of porosity on trapped magnetic field and mechanical stresses in HTS bulks during PFM
\documentclass[conference]{IEEEtran}
\IEEEoverridecommandlockouts
\usepackage{cite}
\usepackage{amsmath,amssymb,amsfonts}
\usepackage{algorithmic}
\usepackage{graphicx}
\usepackage{textcomp}
\usepackage{xcolor}
\def\BibTeX{{\rm B\kern-.05em{\sc i\kern-.025em b}\kern-.08em
T\kern-.1667em\lower.7ex\hbox{E}\kern-.125emX}}\begin{document}\title{Impact of porosity on trapped magnetic field and mechanical stresses in HTS bulks during PFM\
}\author{\IEEEauthorblockN{Santiago Guijosa, Kévin Berger, Melika Hinaje}
\IEEEauthorblockA{\textit{Université de Lorraine,}\
\textit{GREEN} \
F-54000 Nancy, France\
0000-0002-8064-3684, 0000-0001-8841-917X, 0000-0001-5255-2702}
\and
\IEEEauthorblockN{Frederic Trillaud}
\IEEEauthorblockA{\textit{Instituto de Ingeniería,}\
\textit{Universidad Nacional Autónoma de México} \
04510 Ciudad de México, Mexico\
0000-0002-6964-5603
}% \and
% \IEEEauthorblockN{5\textsuperscript{th} Given Name Surname}
% \IEEEauthorblockA{\textit{dept. name of organization (of Aff.)} \
% \textit{name of organization (of Aff.)}\
% City, Country \
% email address or ORCID}
% \and
% \IEEEauthorblockN{6\textsuperscript{th} Given Name Surname}
% \IEEEauthorblockA{\textit{dept. name of organization (of Aff.)} \
% \textit{name of organization (of Aff.)}\
% City, Country \
% email address or ORCID}
}
\maketitle%%%%%%%%%%%%%%%%%%%%%%%%%%%%%%%%%%%%%%%%%%%%%%%%%%%%%%%%%%%%%%%%%%%%%%%%%%%%%%%%%%%%%%%%%%%%%%%%%%%%%%%%%%%%%%%%%%
\begin{abstract}
During pulsed-field magnetization (PFM) processes, high-temperature superconducting (HTS) bulks are subjected to significant mechanical deformations due to rapid changes in magnetic flux (Lorentz force) and temperature (thermal stress), potentially leading to fracture. Furthermore, fabrication-induced defects, such as cracks, pores, and grain boundaries, can strongly impact the HTS performance, often resulting in non-uniform trapped magnetic fields and promoting mechanical failure. The present study assesses the impact of porosity on the trapped magnetic field, temperature, and mechanical stresses through a 2D multiphysics PFM numerical model using COMSOL Multiphysics. The results show that the porosity highly influences both local stresses and the temperature rise by affecting the distribution of induced currents, which leads to an non-uniform trapped magnetic field.\ %These results offer valuable insights into poor trapped field distributions of HTS magnets caused by porosity underscore practical and modeling considerations for their magnetization and modeling and highlight key fabrication factors warranting further investigation.
\end{abstract}\begin{IEEEkeywords}
Electromagnetic analysis, HTS Bulks, porosity, pulsed-field magnetization, coupled thermoelectromagnetic and mechanical analysis.
\end{IEEEkeywords}%%%%%%%%%%%%%%%%%%%%%%%%%%%%%%%%%%%%%%%%%%%%%%%%%%%%%%%%%%%%%%%%%%%%%%%%%%%%%%%%%%%%%%%%%%%%%%%%%%%%%%%%%%%%%%%%%%
\section{Introduction}
HTS bulks can be used in high-field applications as trapped-field magnets. However, the homogeneity and magnitude of the trapped magnetic field highly depend on the material's fabrication ultimately affecting its quality~\cite{Namburi_2021}. Despite advances in manufacturing processes that enhance flux pinning capabilities and homogeneity, such as the top-seeded melt growth (TSMG) and infiltration growth (TSIG), defects like pores and cracks persist. These defects can impact the thermal, and mechanical properties of the bulk and the magnitude of the trapped field~\cite{CambridgePorosity}.The mechanical stresses induced during magnetization, notably in pulsed-field magnetization (PFM), originate from the combination of the Lorentz forces and the thermal induced stresses. They can cause fractures within the brittle ceramic materials. Even though there is substantial modeling and research on mechanical failure~\cite{YANG20171,trillaud}, there is a lack of focus on the impact of the pores on the mechanical behavior of the bulk, its temperature rise, and the value and uniformity of its trapped field during PFM. Hence, the present study proposes to fill the gaps by including the presence of pores in a multiphysics model implementing electromagnetic physics via the $\mathbf{H}$-formulation coupled to mechanical and thermal physics.
%%%%%%%%%%%%%%%%%%%%%%%%%%%%%%%%%%%%%%%%%%%%%%%%%%%%%%%%%%%%%%%%%%%%%%%%%%%%%%%%%%%%%%%%%%%%%%%%%%%%%%%%%%%%%%%%%%
\section{Modeling framework}
In the proposed 2D plane model shown in Fig.~\ref{figPores}, the HTS bulk domain $\Omega_{sc}$ is considered as an infinitely long cylinder encapsulated by an air domain $\Omega_{a}$. The $\Omega_{sc}$ domain includes the presence of pores $\Omega_{p}$ in the shape of small ellipsoids. The external pulsed-field $B_a(t)$, given in~\eqref{eq:magnetic_pulse} is applied along the axial direction of the infinite cylinder at the air boundary $\Gamma_a$.
\begin{equation}
B_a(t) = B_m \frac{t}{\tau} \exp\left(1 - \frac{t}{\tau}\right)
\label{eq:magnetic_pulse}
\end{equation}
where (B_m) is the peak magnetic flux density and (\tau) is the duration required to reach the peak of the pulse.\begin{figure}[t]
\centerline{\includegraphics[width=0.3\textwidth]{pores.png}}
\vspace{-1em}
\caption{Schematic drawing of the different domains and their boundaries: HTS bulk $\Omega_{sc}$, air $\Omega_a$ and pores $\Omega_p$ (blue ellipsoidal inclusions). Note that the pores are scaled and appear larger than they are actually in the numerical model.}
\label{figPores}
\end{figure}%%%%%%%%%%%%%*%
\subsection{$\mathbf{H}$-formulation}
The electromagnetic behavior is modeled by solving for the magnetic field $\mathbf{H}$ according to:
\begin{equation}
\mu_0 \frac{\partial \mathbf{H}}{\partial t} + \nabla \times \left(\rho \nabla \times \mathbf{H}\right) = 0
\label{eq:maxwell}
\end{equation}
where (\mu_0) is the permeability of the vacuum and (\rho) the electrical resistivity of the media. The latter is constant equal to (\rho_{a}) for both $\Omega_{a}$ and $\Omega_{p}$, and it follows the power law model for the superconducting domain $\Omega_{sc}$.%%%%%%%%%%%%%*%
\subsection{Heat Equation}
To evaluate the temperature changes in the superconductor (\Omega_{sc}) caused by the Joule effect (Q = E \cdot J), the following equation is solved,
\begin{equation}
\gamma_m c_p \frac{\partial T}{\partial t} - \nabla \cdot \left(\kappa \nabla T\right) = Q.
\label{eq:heat_equation}
\end{equation}
Here, (\gamma_m) is the mass density, (c_p) is the specific heat capacity at constant pressure, and (\kappa) is the thermal conductivity of the bulk.
%%%%%%%%%%%%%*%\subsection{Mechanical Behavior}
Temperature gradients and Lorentz forces ($\mathbf{F}_L = \mathbf{J} \times \mathbf{B}$) emerge during magnetization inducing strain and stresses in the bulk of the superconductor. The resulting displacement field $\mathbf{u}$ can be solved within the theory of linear elasticity according to,
\begin{equation}
\nabla \cdot \sigma + \mathbf{F}_L = \gamma_m \frac{\partial^2 \mathbf{u}}{\partial t^2}.
\label{eq:mechanical_behavior}
\end{equation}
In this equation, (\sigma) symbolizes the 2D stress tensor related to the total strain (mechanical and thermal) via the Hook's law. The thermal induced strain is given by $\alpha \Delta T$, with $\alpha$ the thermal expansion coefficient.%%%%%%%%%%%%%%%%%%%%%%%%%%%%%%%%%%%%%%%%%%%%%%%%%%%%%%%%%%%%%%%%%%%%%%%%%%%%%%%%%%%%%%%%%%%%%%%%%%%%%%%%%%%%%%%%%%
\section{Results and conclusion}
In the present case, the dependence of the critical current density on local magnetic field and temperature $J_c(\mathbf{B}, T)$ is considered. The HTS bulk has a diameter of 29~mm, with 50 ellipsoidal pores dispersed randomly within its structure. In 2D, these pores constitute approximately 1\% of the bulk's surface area, which is less than the fractions commonly observed in real HTS bulks. The diameters of each pore range randomly between 125-250~$\mu$m with a proper mesh size. The diameter distribution is consistent with that of actual pores. The peak of the applied field is 4~T, with a time constant $\tau$ of 13~ms and parameters corresponding to an operating temperature of 65~K~\cite{TSIG}.Fig.~\ref{figBDis} shows the magnetic flux density distribution at $\tau$ and $10000\times\tau$ to include the thermal recovery ending the magnetization process. The observed phenomenon of uneven and accelerated penetration of the magnetic field at time $\tau$ in the porous case can be explained by the redirection and concentration of current density lines around each pore. This results in a localized increase in both losses and temperature, with a maximum rise of $\Delta T = 25$~K in a few milliseconds. Consequently, in addition to the particular current paths, the presence of pores produces significant magneto-thermal instabilities, which further accentuate the formation of a non-uniform distribution of the trapped magnetic field.
\begin{figure}[t]
\centerline{\includegraphics[width=0.46\textwidth]{BDistv4.png}}
\vspace{-1em}
\caption{Magnetic flux density distributions in the bulk at the peak external magnetic field and at the end of the PFM reaching steady state for the ideal (non-porous) case (a)-(b) and the porous case (c)-(d), respectively.}
\label{figBDis}
\end{figure}\begin{figure}[t]
\centerline{\includegraphics[width=0.45\textwidth]{Untitled.png}}
\vspace{-1em}
\caption{Maximum hoop and radial stress in the superconductor over time for the ideal and porous case. The porosity leads to a higher tensile stress compared to the ideal case. }
\label{figStress}
\end{figure}Fig.~\ref{figStress} shows the maximum hoop and radial stresses over time for the porous and ideal (non-porous) simulations. One can see that, for the porous case, the maximum tensile stresses are significantly greater than the ideal case and occur abruptly during the PFM. For higher applied fields and greater number of pores as well as their distribution, stresses could reach the critical tensile stress of the HTS, which is about $\sigma_c \approx$ 50~MPa.
In the final version of the paper, we will examine the coupled electromagnetic and thermo-mechanical behavior of the superconductor for different porous scenarios, focusing on the possible reduction of the trapped field and stresses that may break the HTS. Several case studies will be used to better understand the underlying mechanism and predict the situations that can lead to the propagation of cracks.
% \section*{References}
\bibliographystyle{unsrt}
%\bibliographystyle{plain}
\bibliography{bib}
\end{document}Speaker: Santiago Guijosa Guadarrama (GREEN-University of Lorraine)
-
5
-
12:00
Lunch break
-
Session 1: Coupled & Uncoupled Multiphysics Problems: C
-
10
Multi-physics modeling of metal-insulated REBCO magnets with screening currents
The design of REBCO high temperature superconducting (HTS) ultra-high-field magnets requires fast and accurate multi-physics modelling (electromagnetic, thermal and mechanical). This contribution presents a novel computationally-efficient multi-physics method that takes screening currents into account. We apply this method to a REBCO insert within a 19 T / 150 mm bore low-temperature superconducting (LTS) magnet. We analyze the electro-thermal quench behavior, the thermal stress during quench, and the axial force on the LTS due to quench in the HTS insert. Results suggest that AC loss from screening currents speed-up electrothermal quench.
Speaker: Enric Pardo (Institute of Electrical Engineering, SAS)
-
10
-
Session 2:Innovative methods and tools for modelling large-scale HTS systems: A
-
11
Modelling a single-layer CORT cable with coordinate transformation
We present a finite element model for a single-layer CORT cable composed of three coated conductors wound around a tube and carrying an AC current. We use a coordinate transformation that takes into account the helicoidal symmetry of the cable and enables the problem to be studied with an equivalent two-dimensional model. We show that this model correctly captures the full three-dimensional pattern of the current flow and allows us to calculate the AC losses as a function of the pitch angle and the length of the gap between conductors. We compare the results with a full 3D model based on the H-formulation and compare the AC losses with well-established analytical formulae.
Speaker: Benoît Vanderheyden (University of Liège, Belgium) -
12
A frequency domain finite element model for simulating high temperature superconductors using the J-A and T-A formulations
AC losses, current density and the magnetic field are important variables for designing high-temperature superconducting (HTS) devices. The preferred method to compute those parameters is the finite element method. In this framework, most of the computational effort has been carried out in the time domain even though the interest may lay in the steady-state regime. For the latter, it is sensible to use a frequency model. This is the proposal here with the implementation of phasors in the modern T-A and J-A formulations. To validate the models, current density distribution and AC losses for the two formulations are compared against time-domain solutions and ultimately against experimental data for single BSCCO and a CORC® cable cooled at 77.3 K in liquid nitrogen.
Speakers: Frederic Trillaud (Universidad Nacional Autónoma de Mexico), Dr Gabriel dos Santos (Electrical Engineering Department, Rio de Janeiro State University) -
13
Influence of ferromagnetic structure addition on the field trapping ability of MgB2 bulk samples
Superconductors have revolutionized magnet technology, surpassing the limitations of traditional coils and permanent magnets. Relying on the results of trapped field measurements carried out on MgB$_2$ discs, in this paper we numerically investigate the field trapping ability of hybrid layouts where ferromagnetic (FM) structures were added to a superconducting (SC) disc. To this aim, through an iterative procedure we first evaluated the critical current density dependence on magnetic flux density that allows reproducing the trapped field measured in the superconductor. Then, this dependence was entered into a numerical model based on the magnetic vector potential A-formulation and employed to calculate the field trapped in different hybrid layouts. The best results were achieved assuming a drilled SC disc filled with a FM bulk disc. The effect of the radius of the FM disc on the field trapping capability of the whole structure was finally investigated.
Speaker: Laura Gozzelino (Politecnico di Torino)
-
11
-
15:00
Coffee Break
-
Session 2:Innovative methods and tools for modelling large-scale HTS systems: B
-
14
Recent Advances in BELFEM and Toward a Community-Driven Material Database for HTS Modeling
We present the latest progress within the
BELFEM project, with a focus on the electromagneticthermal
modeling of high-temperature superconducting
cables and magnets. We discuss a recent validation and
benchmark against COMSOL and GetDP, and provide a
brief outlook onto current fields of research.
A primary challenge encountered in the accurate modeling
of such systems is the representation of material
properties, which are highly nonlinear and sensitive to
variations in magnetic field, temperature, and electrical
current. Based on the experience made in recent investigations,
we propose the development of a community-driven
material database where all datasets are regularized and
provided as B-Spline based lookup tables, thus offering a
fast and efficient way of providing the smooth derivatives,
which are highly beneficial for these nonlinear problems.Speaker: Dr Christian Messe (Berkeley Lab) -
15
Electrothermal modeling of HTS coils using homogenization and different formulations
HTS coils are used in various applications, however, it is complicated and time-consuming to model their multiphysics behavior. We have developed a simple homogenized method to accurately simulate HTS coils, in the context of electrothermal quench. Different numerical models are benchmarked for these computations, and they show very good agreement for different configurations of homogenized method.
Speaker: Anang Dadhich (Institute of Electrical Engineering, Slovak Academy of Sciences) -
16
H-phi Simulations for Pre-Quench and Minimum Quench Energy in HTS Tapes
We introduce a H-phi magneto-thermal model to predict the dynamics of quench nucleation in HTS tapes by finite-element simulations. This superconductor model uses an original interpolation regime between the usual power-law model and the normal state resistivity, based using Bezier curves to allow a smooth transition between these two regimes. It is shown that this explicit modeling of the flux flow regime delays the quench nucleation when compared to the extrapolation of the power law model up the normal state. This helps reduce the non-physical overshoot of the voltage at the terminals of a quenched tape. We also compare the H-phi magneto-thermal simulations with some well-established electro thermal simulations, highlighting the key differences between both models.
Speaker: Gregory Giard (Polytechnique Montreal) -
17
Lumped Parameter Model for Simulation of HTS Cables in Power System Simulators
Due the integration of superconducting technologies into electrical networks around the world, its precise simulations in power grids are increasingly becoming a desirable outcome. Sophisticated methods have been used to model superconducting power cables and, in this way, predict its behavior under different conditions. Most of the available models, however, are not advisable to be used and embedded in power system simulators. In this work, we focus on the development of a method for modelling superconducting cables in traditional power grid simulators. Besides considering the heat transfer conduction in the solid layers, the model also incorporates the transient behavior of the cooling media, which is mandatory for such cables. It has been observed that the proposed model requires less computational effort and is able to deliver accurate results when compared to more advanced methods.
Speaker: Wescley Tiago Batista de Sousa (Karlsruhe Institute of Technology)
-
14
-
19:00
Dinner
-
1
-
-
18
Transfer to the Paul Scherrer Institute by bus
-
Key-note presentations from sponsors Paul Scherrer Institute (PSI)
Paul Scherrer Institute (PSI)
-
19
Implementing user-defined superconductivity formulations with the COMSOL Multiphysics® software in an efficient and reusable way
see Word file
Speaker: Sven Friedel (COMSOL Multiphyiscs GmbH) -
20
Renaissance FusionSpeakers: Diego Pereira, Lucas Blattner
-
21
SigmaphiSpeaker: Emmanuel Voisin
-
22
Fast and scalable Superconductor simulations in the cloud with Quanscient Allsolve
Fast and scalable Superconductor simulations in the cloud with Quanscient Allsolve
Dr. Valtteri Lahtinen, Chief Scientist and Co-Founder
Dr. Janne Ruuskanen, Application Engineer and Superconductor Modeling ExpertSpeakers: Janne Ruuskanen (Quanscient Oy), Valtteri Lahtinen (Quanscient Oy)
-
19
-
10:20
Coffee Break Paul Scherrer Institute (PSI)
Paul Scherrer Institute (PSI)
-
Poster Session Paul Scherrer Institute (PSI)
Paul Scherrer Institute (PSI)
-
23
3D Modelling and Magnetization Losses in CORC-TSTC hybrid composite conductors
The so-called Conductor On Round Core (CORC) and the Twisted Stacked-Tape conductor (TSTC) are both the most compelling candidates for the development of high temperature superconducting (HTS) cables, both with the high current carrying capabilities required for the future development of fusion projects, with the CORC cross-sectional design being generally larger than its TSTC counterpart. In this sense, to solve the spatial inefficiency in the former volume of the CORC conductor and solve the limitation of the conductive current of the TSTC, whilst remaining true to the CORC dimensions, the feasibility to manufacture a CORC-TSTC hybrid cable has been proven by a team of Korea researchers, where their measurements of current density and AC losses are yet to be validated by the scientific community. Thus, in this paper, we perform a comprehensive electromagnetic study validating the experimentally measured AC-losses of a series of CORC-TSTC hybrid cables under external magnetic field, utilizing a three-dimensional simulation environment capable to account for the 3D current dynamics inside the HTS tapes, and not only on a mathematically reduced and virtually homogenised 2D surface where the loops of magnetization currents can be incoherent with the well stablished physics of the Bean’s mechanism. The cables will be modelled under the base of a six-tapes single layer CORC cable with the former made of analogous stacked HTS tapes produced by SuNAM Co., Ltd. The study will consider the impact of the increment of stacked layers in the TSTC former, running from one to up to four stacked tapes and, the influence of the acute magneto-angular anisotropy of the GdBCO tapes, which will be brought forward from additional experimental measurements that will ensure a proper benchmark for the validation of the experimentally measured AC-losses in these hybrid cables.
Speaker: Hasan Al-ssalih (University of Liecester) -
24
HTS superconducting magnetic energy storage (SMES) for waterborne applications
The shift from fossil fuel to electric based propulsion in the waterborne transport sector has been sped up by recent policies aiming to reduce the sector emissions. This trend creates highly electrified vessels, with needs for energy storage systems (ESS) to satisfy the power demand affordably and to increase the on-board grid reliability and efficiency. Initial industry efforts have been put in the study and integration of high energy density ESS solutions, mainly electrochemical batteries. However, other innovative ESS, with different capabilities, have not been yet fully addressed. It is the case of Fast Response Energy Storage Systems (FRESS), such as Supercapacitors, Flywheels, or Superconducting Magnetic Energy Storage (SMES) devices. The EU granted project, POwer StoragE IN D OceaN (POSEIDON) will undertake the necessary activities for the marinization of the three mentioned FRESS. This study presents the design process followed in the POSEIDON project for the definition of an SMES suitable for maritime operation, which will be based in High Temperature Superconductors (HTS). The electromechanical model of the SMES will be presented starting with the tape modeling, and the calculation of the electromagnetic forces, including the screening currents. Finally, the electromechanical analysis, including the working point of the magnet and the stress analysis of the coil will be presented.
Speaker: Carlos Gil Boronat -
25
Mechanical-electric behaviors of CORC cable under different deformation modes
Please see the attachments
Speaker: Prof. Yuanwen Gao (Lanzhou University) -
26
Stress, strain and mechanical analyses of REBCO superconducting tapes using finite element method.
Abstract— High-temperature superconducting (HTS) tapes, represented by Rare Earth-Barium-Copper-Oxide (REBCO) conductors, are promising for high energy and high field superconducting applications. However, practical applications subject HTS conductors to various stresses and strains, including residual stresses due to thermal mismatch and tensile stresses from Lorentz forces. This can result in reduced load-carrying capacity and the risk of electromechanical properties degradation. Investigating the mechanical behavior of REBCO tapes under different tension loads is necessary to properly understand the stress-strain distribution inside the layered structure. However, assessing the mechanical properties of each HTS component presents unique challenges due to their brittle nature, sensitivity to environmental conditions, and complex layered structure. This study demonstrates how Finite Element Method (FEM) simulations, combined with experimental tests, can effectively describe the mechanical behavior of each component in a laminated superconductor tape.
Keywords—HTS, FEM, COMSOL, mechanical propertiesI. INTRODUCTION
High temperature superconducting Rare Earth-Barium-Copper-Oxide (REBCO) conductors hold significant promise for a range of energy and high magnetic field applications like power cables, generators, fusion, accelerators, medical devices. This is primarily due to their high critical temperature and critical current density even in the presence of a high background magnetic field [1]. REBCO coated conductors (CC) are composed of layered materials, featuring multiple laminated high-aspect-ratio (HAR) layers with distinct material properties [2]. This layered structure includes a substrate, a stack of buffer layers, the REBCO layer, and stabilizing layer(s). Notably, in CC, the substrate and stabilizer(s) are substantially thicker than other functional layers, significantly influencing the mechanical and electromechanical properties of the superconducting wire under tension. In addition, a CC is composed of very different types of materials including soft metals, brittle ceramics and hard metal alloys. Serving as the backbone of the tape, the substrate acts as the mechanical foundation for the other layers. Different manufacturers employ various substrate materials such as Hastelloy and stainless steels, each with unique mechanical properties. Stabilizing layers, typically a layer of copper on top of a thin silver layer, are applied using techniques like electroplating for the first and sputtering for the second. These layers not only offer protection during the transition from superconducting to normal state but also reinforce the mechanical integrity of the superconductor tape. While the mechanical behavior of commonly used substrate and stabilizing layer materials is well-understood, analyzing the mechanical properties of thinner layers like the REBCO layer and stacked buffer layers poses a more complex challenge. These layers, characterized by extreme HAR and brittle behavior, are challenging to isolate and study. Their mechanical behavior within the complete CC structure is hindered by their reduced thickness compared to the primary layers. This study illustrates how Finite Element Method (FEM) simulations accurately represent stress-strain distribution in each individual layer, starting from experimental analysis of coated conductor superconducting tapes under uniaxial tension.II. EXPERIMENTAL SETUP
The REBCO tape considered were made by Fujikura. The tape has a width of 12 mm while the layered structure is divided in a Hastelloy substrate of 50 μm thickness, a buffer layer of 0.2 μm thickness, a REBCO layer of 2 μm thickness and finally a copper layer of 20 μm surrounding the whole tape. Typically, a silver protective layer of 2 μm thickness is placed at the interface between REBCO and copper, in this work the protective layer has been omitted due to its negligible mechanical influence [3].
Tensile tests are performed at room temperature using a servo-hydraulic testing machine, an end of the tape is locked into a fixed clamp while the other end is locked into a clamp free to move vertically. A load cell constantly records the applied load, while the strain is studied using Digital Image Correlation (DIC). DIC is an optical method that employs image registration and tracking techniques to analyze and compare the variation of the position of different points on the sample surface and from those derive the displacement field during the deformations [4]. A scheme of the experimental setup is shown in Fig. 1.III. NUMERICAL MODEL
To evaluate the stress-strain distribution generated in each one of the tape component FEM simulation software COMSOL Multiphysics was employed.
The main challenge related to simulate the superconductor layered structure is the great difference in the thickness of each component. The typical meshing considered for simulations, the tetrahedral meshing, would require a high density of domain elements at the interface between REBCO/buffer layer and other components to properly compute the interaction of finer elements with the thicker one. This method would lead in general to more complex and more expensive simulations in terms of computational time. Therefore, we considered a mapped mesh of squared elements that does not require the clustering of domain elements in specific areas. This process allows to better control the refinement of the mesh, leading to more accurate results in less computational time.
The first set of simulations considered compare the stress-strain distribution generated in two tapes, the first one composed only of substrate and the copper stabilizer while in the second one also the REBCO and buffer layers were considered.
The second set of simulations instead compares the mechanical response of a full tape and a tape where the buffer layers are absent.
The geometry considered for both simulations have a width of 6 mm and a length of 2 mm. Due to the spatial symmetry of the structure and boundary conditions, the bottom edge and the axis of the tape are represented as symmetry plane, allowing to simulate only a quarter of the interested region.IV. RESULTS
As is possible to observe in Fig.2, the comparison between the first set of simulations confirms that the REBCO layer does not affect the stress-strain distribution generated in the main layers of the tape. This result allows to further simplify the numerical model considered. It is indeed possible to neglect the effect of the REBCO layer when interested in the overall mechanical properties of the whole tape, while it is possible to employ a unidirectional coupling by applying the strain distribution calculated in the substrate and the stabilizer to the REBCO layer when interested in a more locally focused mechanical behavior.
Similar results are obtained from the second set of simulations. In both case the REBCO layer shows the same stress-strain distribution, meaning that the buffer effect on the superconducting layer is negligible and they can be computed as a single layer with uniform mechanical properties, allowing for a further simplification of the numerical model.
V. CONCLUSIONS
In this work we employed finite element simulations to represent the mechanical response generated in the layered structure of a superconductor tape under uniaxial tension.
We compared the stress-strain distribution inside each component considering different layers combinations to understand their relative influence. The preliminary results show that the main structural component of the tape, the substrate and the stabilizer are unaffected by the thinnest layers, and in a similar way the buffer layer has a negligible impact on the REBCO layer. Both results allow to decrease the complexity of the simulations considered, decreasing the general computational cost while maintaining accurate results.ACKNOWLEDGMENT
Authors acknowledge the support RTI2018-095853-B-C21 SuMaTe, PID2021-127297OB-C21 SUPERENERTECH, and Severo Ochoa CEX2019-000917-S projects from MICINN and co-financing by the European Regional Development Fund; 2017-SGR 1519 from Generalitat de Catalunya and COST Action Hi-SCALE from EU. We specially thank Fujikura for the samples supply.REFERENCES
[1] Larbalestier D, Gurevich A, Feldmann D M and Polyanskii A, 2001 High-Tc superconducting materials for electric, power applications Nature 414 368–77.
[2] Obradors X and Puig T 2014 Coated conductors for power applications: materials challenges Supercond. Sci.Technol. 27 044003.
[3] Y. Zhang et al., "Stress–Strain Relationship, Critical Strain (Stress) and Irreversible Strain (Stress) of IBAD-MOCVD-Based 2G HTS Wires Under Uniaxial Tension," in IEEE Transactions on Applied Superconductivity, vol. 26, no. 4, pp. 1-6, June 2016,
[4] Konstantopoulou, Konstantina (2015). Mechanical behavior of 2G REBCO HTS at 77 and 300 K. Thesis (Doctoral), E.T.S.I. Caminos, Canales y Puertos (UPM)
[5] Gao, P., Chan, W.-K., Wang, X., Zhou, Y., and Schwartz, J., “Stress, strain and electromechanical analyses of (RE)Ba2Cu3Ox conductors using three-dimensional/two-dimensional mixed-dimensional modeling: fabrication, cooling and tensile behavior”, Superconductor Science Technology, vol. 33, no. 4, IOP, 2020Speaker: Luca Benedetti (ICMAB) -
27
Study of a New Axial-Field Superconductor Inductor for a Synchronous Machine
Abstract— In this work, a new topology of an inductor of axial flux synchronous machine is presented and tested. It is executed by combining superconducting (SC) bulks and six solenoids. It consists of six superconducting solenoids connected in series stuck in a non-magnetic disc and supplied by direct current. The presence of two SC bulks which by their magnetic field screening property, modulate and redirect the flux density lines produced by the six solenoids . Thus, we can generate a periodic spatial variation of the axial flux density component.
A 3D Electromagnetic modeling based on finite elements solution is developed to demonstrate the suitability of using the magnetic shielding properties of the SC bulks. In order to check the screening properties of the SC bulk, a prototype of the proposed inductor has been constructed at the laboratory. it consists of six copper solenoids and two circular shape superconducting YBCO bulks.
Keywords—Axial machine, Magnetic Field concentration,Superconducting Inductor, Superconductor machine.
I. INTRODUCTION
The advances in the technology of superconducting materials and cryogenic systems are at the origin of a new generation of electric actuators. Indeed, the use of superconductors allows to generate very intense magnetic fields and to transmit energy without losses 1.
One of the main challenges to use of superconductors in electrical machines is increasing the flux density in the air gap and therefore reduces the volume of the electrical machine 3.
Various topologies of synchronous machines have been realized with inductors excited by superconductor coils. In synchronous machines with axial flux, the magnetic field is directed along the axis with "flower petal" windings. Several structures have been realized, distinguishing three categories, machines with superconducting coils, others with passive superconducting materials (bulks) and machines with both types of the materials [1,5].In this work, a new topology of an inductor of an axial-field synchronous machine is presented and constructed in the laboratory. It is executed by combining SC bulks and solenoid. This inductor, as shown in figure.1, is made up of six superconducting solenoids connected in series stuck in a non-magnetic disc supplied by direct current. The presence of two SC bulks which by their magnetic field screening property, modulate and redirect the flux density lines produced by the solenoids [5,6].Thus, we can generate a periodic spatial variation of the axial flux density component. In fact, each HTC superconducting bulks placed on the non-magnetic disk (inductor) cooled with liquid nitrogen constitutes a barrier against the passage of the flux density lines created by the superconducting solenoids [4,2].
II.ELETROMAGNETIC MODELING
In order to study the feasibility of this new topology inductor of synchronous machine, a 3D Electromagnetic modeling based on finite elements solution is developed. The model was solved in magneto-static without induced currents. Using a magnetic vector potential formulation, noted A, the flux density B is defined by:
B = ∇×A....................................(1)
The PDE to solve in the different regions parts of the inductor is:
In the air and the superconducting bulks: ∇A^2 = 0..........(2)
In the solenoid: ∇A^2 = -μ0 μrJ.............................(3)
It is considered in this modeling that the superconducting solenoids is supplied by a uniform current density across their sections area and low relative permeability μr=10^(-4) of the SC bulk to take into account its screening property.The magnetic potential is taken as zero on the surfaces of a box encompassing the structure of the inductor and the armature.
The developed 3D elements finite model is simulated for the proposed inductor with superconducting solenoids supplied by DC current with a density of 743.17 A/mm2.
It can be seen in figure .2 that the axial flux density component predicted by the 3D developed model has a periodic spatial variation and its amplitude varies between positive Bmin and Bmax values. The maximum value reaches 3.3T.
In figure .3, we can clearly see the screening effect of the two SC bulks.
III. EXPÉRIMENTAL RESULTS
A prototype of the proposed inductor has been constructed in the laboratory. As shown in Fig. 4, it consists of six solenoids connected in series with the copper and two circular shape superconducting bulks.The SC bulk is made from YBCO material. The critical temperature of this superconductor is 93K. This inductor is cooled with liquid nitrogen to 77K.The test is carried out by supplying the solenoid with DC current of I=8.45 A. It can be seen in figure.5 that the flux density waveform predicted by the 3D developed model is in a good agreement compared to the experiments.The maximum of flux density measured in the air gap reaches 36.8 mT.
IV CONCLUSION
A new topology of an inductor of axial flux synchronous machine is presented in this work. It consists of superconducting solenoid supplied by direct current and two superconducting bulks which by their magnetic field screening property, allows to generate a periodic spatial variation of the axial flux density component.
A prototype of the proposed inductor consisting of a copper solenoid and two superconducting YBCO bulks has been developed and constructed in the laboratory.
The results obtained by 3D FE and experiments are in good agreement and they show the feasibility of the new topology of the proposed inductor. Thus, with superconducting solenoid it is possible to considerably increase the fluxdensity in the air gap and therefore reduce the volume of the electrical machine.
REFERENCES
1 EH. Ailam, MN. Benallal, M. Hachama, J. Leveque and A. Rezzoug, "Comparison Study Between Several Solutions of Superconducting Inductors," in IEEE Transactions on Applied Superconductivity, vol. 23, non. 1, pp.5200506-5200506, février 2013.
2 M. Kelouaz, Y.Ouazir and L. Hadjout, "3D Magnetic field modeling of a new synchronous machineusingnetwork method reluctance"Physica C: Superconductivity and its Applications, Volume 548, Mai 2018.
3 K. F. Goddard, B. Lukasik and J. K. Sykulski, "Alternative Designs of High-Temperature Superconducting Synchronous Generators," in IEEE Transactions on Applied Superconductivity, vol. 19, no. 6, pp. 3805-3811, Dec. 2009.
4 R. Alhasan,T. Lubin , J. Leveque , Study and test of a new superconducting inductor structure for a synchronous machine, in: International Conference on Electrical Sciences and Technologies in Maghreb (CISTEM), Tunis, 2014, pp. 1–7. 3-6 Nov.
5 P. J. Masson, C. A. Luongo “High Power Density "Superconducting Motor forAll-Electric Aircraft Propulsion", IEEE Transactions on Applied Superconductivity, Volume15, Issue 2, Part 2, June 2005 Page(s):2226 – 2229.
[6] D. Netter, J. Leveque, E. Ailam, B. Douine, A. Rezzoug and P. J. Masson, "Theoretical study of a new kind HTS motor," in IEEE Transactions on Applied Superconductivity, vol. 15, no. 2, pp. 2186-2189, June 2005.Speaker: Dr hakim douar (Université des Sciences et de la Technologie Houari Boumediene Algérie) -
28
Study on stability of high temperature superconducting magnet in fusion reactor under nuclear heat condition
China Fusion Experimental Reactor (CFETR), European Fusion Reactor (EU DEMO), and US Fusion Reactor (SPARC) are all actively developing high-temperature superconducting magnet (HTS) design schemes to effectively improve the magnetic field strength of future fusion reactors and increase fusion power. The resulting fusion nuclear heat effect brings great challenges to the stability of superconducting magnets. Taking CFETR as an example, the nuclear heat of toroidal field magnets caused by fusion neutrons on the side facing the plasma reaches 122.74 W·m-2. Therefore, it is particularly important to evaluate the critical characteristics of HTS in nuclear heat conditions efficiently and accurately, and to ensure its sufficient stability margin.
Burning Plasma Experimental Superconducting Tokamak (BEST) is a new type of tokamak device developed in China for the realization of deuterium-tritium fusion. In response to the nuclear heat stability of the BEST superconducting magnet system, the project team has carried out a series of research. The critical properties of high-temperature superconducting magnets are affected by factors such as temperature, magnetic field, and strain. First, based on electromagnetic analysis, the magnetic field distribution of the conductor is obtained. Then, based on Monte Carlo particle transport calculations, the nuclear heat distribution of the magnet system is obtained. Finally, based on cooling design, thermal engineering analysis is carried out. For various operating modes of BEST (induction operating mode, hybrid operating mode, and steady-state operating mode), a multi-heat source loading program is developed to achieve the segmented loading of conductor thermal load over space-time. At the same time, for the problem of temperature margin analysis under unsteady heat transfer, the magnetic field distribution and thermal load spatial distribution are coupled to realize dynamic temperature margin calculation of the conductor. The results show that the temperature margin of the high-temperature superconducting conductor is greater than 10.1K.Speaker: Jinxing Zheng (Institute of Plasma Physics, Hefei Institutes of Physical Science, Chinese Academy of Sciences) -
29
Electromagnetic-mechanical simulation of screening current, field, strain, and voltage
Here we report an electromagnetic-mechanical simulation model to calculate screening current, mechanical stress/strain, magnetic field, and coil voltage. We designed, fabricated, and tested a 20-turn dry-wound REBCO test coil. The coil operated in the cold bore of a 15 T background magnet, deliberately positioned off-centered to induce large screening currents. The coil was exposed to axial and radial fields of 13 T and 0.5 T, respectively, and charged up to 390 A. As a result, we observed a >0.4% strain and subsequent critical current degradation. The proposed model successfully reproduced the measured strains and was used to evaluate over-strain-dependent plastic damage, showing good agreement with the measurements. We believe the proposed model offers a viable option for high-field and high-stress REBCO magnet design and analysis, potentially even upon quench simulation.
Speaker: JESEOK BANG -
30
Homogenization of HTS Coils and Stacks Using the Foil Conductor Model
Homogenization techniques are appealing in reducing the computational cost of simulating structures with many stacked high temperature superconductor (HTS) tapes. In this contribution, the foil conductor model is extended to HTS applications with insulated conductors. The model is derived in 2-D with the A−formulation and allows directly imposing the current in the conductors. Preliminary numerical results are presented to verify the model and to ensure that the model constraints are satisfied.
Speaker: Mr Elias Paakkunainen (TU Darmstadt) -
31
Magnetic field stability of a HTS insert large-scale prototype for a future 33 T CSM magnet
This abstract presents the magnetic field dynamics of a
large-scale prototype of a HTS insert when powered with a
constant transport current. The use of a 2D electromagnetic model
helps to identify the contribution of the changes of current
distribution inside the superconducting layers affecting the
stability. The existence of coupling currents dumping through
resistive interfaces between tapes is also altering the magnetic field
stabilitySpeaker: Alexandre ZAMPA (Tohoku University) -
32
Research on the dynamic multi-heat load coupling calculation method for fusion superconducting magnets
The superconducting magnet system is a key component of the tokamak fusion reactor for confining high-temperature plasma. High-temperature superconducting magnets are favored by various countries due to their larger critical temperature and critical magnetic field. When high-temperature superconducting magnets are applied to fusion devices, they will be subject to various steady-state and transient thermal disturbances, which will lead to the degradation of their critical performance. Based on a compact tokamak device currently being designed in China, we have conducted research on the impact of transient thermal disturbances, including AC loss, nuclear heat, and coil case conduction heat, on the temperature margin of the superconducting magnet system. For AC loss, we considered coupling loss and hysteresis loss, and calculated their time distribution and spatial distribution using empirical formulas. For nuclear heat, we established a detailed winding pack neutronics model and evaluated the spatial distribution of the nuclear heat power of each component based on the Monte Carlo method. For coil case conduction heat, we used a quasi-three-dimensional method and analyzed it using thermal-hydraulic software. Furthermore, based on the cooling circuit design, we developed a multi-heat load time-space coupling loading program to realize dynamic thermal load coupling analysis of fusion superconducting magnets, and finally completed the temperature margin analysis of the toroidal field superconducting magnet and the poloidal field superconducting magnet.
Speaker: Yudong Lu -
33
Holistic numerical simulation of a quenching process on a real-size multifilamentary superconducting coil
Superconductors play a crucial role in the advancement of high-field electromagnets used for particle accelerators, magnetic resonance imaging, fusion reactors, and many other high-end technological applications. Unfortunately, their performance can be compromised by thermomagnetic instabilities, wherein the interplay of rapid magnetic and heat diffusion can result in catastrophic flux jumps eventually leading to irreversible damage. This issue has long plagued high-$J_c$ Nb$_3$Sn wires at the core of high-field magnets. Moreover, the stochastic nature of these magnetic flux avalanches poses a serious challenge to the development of prevention measures such as quench detection criteria. In this study, we introduce a groundbreaking large-scale GPU-optimized algorithm aimed at tackling the complex intertwined effects of electromagnetism, heating, and strain acting concomitantly during the quenching process of superconducting coils. We validate our model by conducting comparisons with magnetization measurements obtained from short multifilamentary Nb$_3$Sn wires and further experimental tests conducted on solenoid coils while subject to ramping transport currents. Furthermore, leveraging our developed numerical algorithm, we unveil the dynamic propagation mechanisms underlying thermomagnetic instabilities (including flux jumps and quenches) within the coils. Remarkably, our findings reveal that the velocity field of flux jumps and quenches within the coil is correlated with the amount of Joule heating experienced by each wire over a specific time interval, rather than solely being dependent on instantaneous Joule heating or maximum temperature. These insights have the potential to pave the way for optimizing the design of next-generation superconducting magnets, thereby directly influencing a wide array of technologically relevant and multidisciplinary applications.
Speaker: Prof. Cun Xue (Northwestern Polytechnical University) -
34
Improvements of Partial Element Equivalent Circuit model of High-field HTS coils
HTS coils used for high field magnets are usually made of several metal-insulated or non-insulated HTS pancakes. Quench modeling of these coils requires time-dependent simulation of current distribution inside each pancake. Partial element equivalent circuit is well-known method of modelling HTS coils, however due to large number of magnetically coupled elements, it can be time and memory consuming, which can limit the accuracy and space/time resolution of the obtained results.
This publication investigates the possibilities of improvements of PEEC method: first step is homogenization, which decreases the number of elements, after that following improvements are added : 3D finite element thermal and mechanical model, axial variation of magnetic field in each element is taken into account. This publication investigates the impact of these improvements on model accuracy and computation time.Speaker: Nikola Jerance (CEA Paris Saclay) -
35
Modeling an HTS Cable with a Superconducting Fault Current Limiter in MATLAB/SIMULINK for Integrating in Electric Aircraft
Aviation electrification is at the center of attention in reducing CO2 emissions. Aircraft are responsible for around 2.4 % of the annual global carbon emissions. This is the motivation behind the development of fully electric, zero-emission aircraft. The advantages of superconductivity, including compactness, lightweight, and high efficiency, make this technology a promising choice to accelerate the transition to electric aviation. A large electric aircraft's powertrain includes motors, converters, DC and AC cables, batteries, fuel cells, fault current limiters, power generators, and fuel storage. This work focuses on modeling two components: resistive superconducting fault current limiter (RSFCL) and HTS DC cable. The adiabatic and non-adiabatic, electrical-thermal lumped-parameter models of the RSFCL are developed in MATLAB. In addition, a configurable MATLAB SIMULINK model of the fault limiter is designed for integration with wider systems models. Moreover, three electrical-thermal models of the HTS DC cable are explained and compared: lumped parameter (0-D), one-dimensional (1-D), and two-dimensional (2-D). Considering the 2-D model as the most credible, the comparison results show that in the case of events (e.g., fault), the lumped-parameter is a suitable and fast short-term solution (during fault). In contrast, in the long-term (after fault), the 1-D and 2-D models are preferred solutions. The results also show that the longer the cable, the higher the credibility of the 2-D model over the 1-D model. A SIMULINK cable model is designed using the lumped-parameter method to simulate its behavior during fault. The designed SIMULINK models of RSFCL and cable give users a high advantage of adjustability and adaptability. Finally, the simulation of a network consisting of these two components in SIMULINK is discussed. The results show the successful performance of the RSFCL to limit the fault current and protect the cable from quench.
Speaker: Mr Ali Khonya (Karlsruhe Institute of Technology (KIT)) -
36
Modelling of Electrical, Magnetic and Thermal Issues for a Non-Insulated HTS-CCT Dipole Magnet
The no-insulation (NI) coil technique has proven to be robust for realizing high-field magnets with REBCO high-temperature superconductors (HTS). While the stable operation and charging delay — both originating from the inter-turn current transfer — on one hand, ensure the success of NI coils, on the other hand, they limit their application scenarios. A possible solution to the charging delay issue is to power the coil with additional current, which could be achieved through either pre-simulation or active feedback control. However, apart from the additional Joule heating that may disturb the stable operation of a REBCO NI magnet, the inter-turn current may also deteriorate the field quality, which can be particularly problematic for an accelerator magnet. These issues, along with uneven current distribution among different turns and the screening current generated inside the HTS ceramics, could be even more critical. Despite these doubts, we believe it is still too early to directly forbid the NI technique on accelerator magnets.
At IHEP, we started to explore the feasibility of employing the NI technique in accelerator magnets since last year. The first step is to eliminate the field delay and realize the target field as we designed. To achieve this, we are developing two methods to simulate the current that should be charged to an NI coil to get the target field, as an alternative way of the dynamic feedback control. The relevant simulation and experiment results on a few small testing coils will be presented, which show a perfect charging of the magnetic field as we desired. Then, the recent progress on the modelling of a canted-cosine-theta REBCO dipole magnet will be presented, regarding the electrical, magnetic, and thermal characteristics during the charging of such a magnet using a multi-physics model that couples circuit grid, magnetic field, and heat transfer analyses.
Speaker: Rui Kang (Institute of High Energy Physics, Chinese Academy of Sciences) -
37
3-D modelling and experimental results of a sorted bulk staggered array undulator
This work presents the 3-D modelling and measurements of the sorting of a 10 cm long high-temperature superconducting bulk undulator. We use the H-ϕ formulation together with the matrix method to produce an inverse analysis of the trapped field potential of each bulk. The simulation results are then used to sort the bulks in order to reduce the field error. A factor of 1.8 error reduction was measured experimentally.
Speaker: Alexandre Arsenault (PSI - Paul Scherrer Institut) -
38
Design, construction and test in SULTAN of high-current ReBCO racetrack coil
Various quench detection methods are under development at EPFL Swiss Plasma Center, aiming at the detection response determined solely by temperature and not affected by EM noise or mechanical strain. This can be especially useful when applied to HTS coils. Currently, the promising options are twisted-pair SQDs (essentially, co-wound insulated superconducting wire), thermocouple chains and FBGs (Fiber Bragg Grating) inserted in Teflon tubing. The performance of the proposed methods is being investigated in SULTAN on a high-current ReBCO racetrack coil. The coil design is based on laminated stacked-tape soldered (LASSO) conductor using 12 tapes of 4 mm width arranged in 6 parallel 2-tape stacks. The coil is wound using an 18 m-long LASSO conductor and fiberglass cloth for turn insulation. It is impregnated with aqueous DMSO providing superior thermal conductivity (up to ~2 W/m/K at 10 K) compared to common solutions such as epoxy or wax, and cooled indirectly by forced-flow helium in steel pipes placed near the coil. In addition to the quench detection instrumentation, the sample is also equipped with CERNOX temperature sensors, hall probes, strain gauges and foil heaters. It is characterized in SULTAN using a 15 kA/10 V direct drive test insert, which allows investigating fully developed quench situations in a controlled manner. This paper gives the details of the sample design and construction, focusing on its intensive instrumentation, and summarizes the main test results in terms of DC, AC and quench performance.
Speaker: Nikolay Bykovskiy (EPFL SPC) -
39
Evaluation of techno-economic aspects of HTS HVAC Transmission Cables by Critical Current Grading Across Phases
Alternative technologies for transmission cables have gained both scientific and industrial interest in recent years. In fact, global electricity production is planned to increase, causing grid nodes to be very much congested. Therefore, these alternative conductors might efficiently transport relevant amounts of power between the nodes. In such a context, superconducting cables are considered a promising solution: they can carry large amounts of energy with minimal losses and compact dimensions. Hence, there would be benefits for the environment as well. To evaluate whether superconducting cables can be integrated in existing grids, techno-economic approaches should be adopted. Such approaches enable the conceptual design of a specific cable architecture. In this way, users can explore a wide range of operating parameters to optimize designs.
This paper reports a comprehensive techno-economic analysis of HVAC cables realized with High Temperature Superconducting (HTS) tapes. The goal is to carry a very high power. The optimal co-axial design is selected by means of OSCaR: this tool allows a graded approach to the critical current of the tapes across different phases. The optimization aims at most effectively balancing tape costs and electrical properties. The main equations of the model, the materials parameters and the applied constraints are reported. The model is then applied to assess how much the length, the carried power and the per unit length cost of the HTS tape impact on the overall cost of transmission lines.Speaker: Gabriele Fornasier (Ricerca sul Sistema Energetico - RSE S.p.A.) -
40
The development of multi-scale method for simulating large-scale REBCO-based coils
The multi-scale method for calculating AC loss of large-scale REBCO-based coils has been proposed for several years. I am one of the researchers contributing to the development of the multi-scale method to enhance its calculation capability. In this presentation, the development of the multi-scale method will be introduced, in which one can find the detailed modelling strategy of the method based on H and T-A formulations, the extension of the method from 2D to 3D models and how the method is employed to simulate large-scale HTS coils with complex geometry.
Speaker: Lei Wang (Institute of Plasma Physics, Chinese Academy of Sciences) -
41
Understanding AC Losses in state-of-the-art superconducting cables: Physics Insights from 2D to 3D computational modelling
Producing accurate computational models that forecast the alternating current losses associated with cold-dielectric conductors is pivotal for power grid investors, what in turn can influence the designing and manufacturing of lightweight superconducting cables aspiring to reach high engineering current densities whilst maintaining a compact structure. By utilizing the so-called H-formulation of Maxwell’s equations with different critical current density approaches, such as a constant Jc model equivalent to the classical but widely successful critical-state model for type-II superconductors, or tailored Jc (B) functions similar to the acclaimed Kim’s model for non-isotropic superconductors, and the most realistic approaches considering the magneto-angular anisotropy Jc (B, θ) of commercial superconducting tapes, we present an extensive electromagnetic analysis for practical cold dielectric conductors, including single phased multi-layer powered cables, triaxial cables, and the state-of-the-art Conductor on Round Core (CORC) and Twisted Stacked-Tape Cables (TSTC) designs. All cables are simulated either within two- or three-dimensional approaches depending on the availability of proper experimental data considering transversal applied magnetic fields and transport currents in the fully assembled cables. Computational results are duly validated by straight comparison with experimental measurements of AC losses, providing further insight on the cumbersome coexistence of magnetization and transport currents inside the superconducting tapes within hysteretic conditions, whose physics can only be resolved within the H-formulation at the expense of increased computational costs. Remarkably, features such as the need to unbalance the current phase distribution in triaxial cables for achieving nearly zero magnetic leakages is shown without the need for recurring to 3D formulations, whilst physically meaningful distributions of current density for both CORC and TSTC cables are shown within our 3D models. Distinctively, CORC cables shows distributions of current density characteristic of Bean’s model with well-defined loops of magnetisation currents turning across the thickness of the superconducting tapes, whereas the TSTC cables exhibit distinctive slab-like profiles due to the twisting of stacked tapes, which also reduces the magnetic flux coupling and consequently its AC losses. In conclusion, this paper serves as a benchmark for comparing the electromagnetic performance and actual physics behind different HTS cabling techniques, offering valuable insights for future development.
Speaker: Harold Ruiz (University of Leicester)
-
23
-
12:10
Lunch Break Paul Scherrer Institute (PSI)
Paul Scherrer Institute (PSI)
-
Session 2:Innovative methods and tools for modelling large-scale HTS systems: C Paul Scherrer Institute (PSI)
Paul Scherrer Institute (PSI)
-
42
Introduction of the magnetic scalar potential $\phi$ in the T-A and J-A formulations for efficient electromagnetic simulations of High Temperature Superconductors
Superconducting devices are likely to play a crucial role in the energy transition addressing power generation, transmission, distribution systems, transportation and even quantum computing. Therefore, developing models that enable fast and highly accurate simulations is important for advancing the technology. This work introduces the \textbf{T}-\textbf{A}-$\phi$ and \textbf{J}-\textbf{A}-$\phi$ formulations in 2D, offering the potential to reduce the number of degrees of freedom by modeling the non-conductive parts of a device using magnetic scalar potential. The coupling between the \textbf{A} and $\phi$ formulations is key for this approach and is detailed in the text. The case studies are a single 2G HTS tape and a CORC\textsuperscript{\textregistered}~cable. The formulations are compared in terms of AC losses, the distributions of magnetic flux densities, and current densities. The validation is carried out using experimental data of AC losses. The results are in good agreement. The key parameter for achieving high accuracy is the boundary mesh between the \textbf{A} and $\phi$ domains.
Speakers: Gabriel dos Santos (State University of Rio de Janeiro), Frederic Trillaud (Universidad Nacional Autónoma de Mexico) -
43
A physic-guided recurrent machine learning model for long-time prediction of quench dynamics
This work presents a PGRML model for predicting superconducting tape temperature profiles during a quench. The model accurately forecasts the nonlinear dynamics involved in a drastically reduced computational time with respect to finite element models.
Speakers: Prof. Frédéric Sirois (Polytechnique Montreal), Nicolas Breault (Polytechnique Montréal)
-
42
-
44
Overview of the Paul Scherrer Institute Paul Scherrer Institute (PSI)
Paul Scherrer Institute (PSI)
Speaker: Hans Braun (Paul Scherrer Institute (PSI)) -
15:00
Coffee Break Paul Scherrer Institute (PSI)
Paul Scherrer Institute (PSI)
-
Session 3: Applications: A Paul Scherrer Institute (PSI)
Paul Scherrer Institute (PSI)
-
45
How to increase the field gradient produced by a superconducting Halbach array by modifying its geometric parameters?
Halbach arrays made of bulk melt-textured YBa2Cu3O7-δ superconductors are very promising systems to generate magnetic flux density gradients exceeding those given by classic Halbach arrays using permanent magnets. When assembling an array made of bulk superconductors, the challenge is to prevent a reorganization of induced currents in the superconductors and their subsequent demagnetization. In this work, we investigate various configurations to achieve this goal: the peripheral samples are replaced by bulk superconductors in the shape of triangular prisms or they are vertically shifted with respect to the central sample. Using 3D finite element modelling and semi-analytical modelling based on Biot-Savart law, we show that very little demagnetization occurs in these structures. Their properties can therefore be predicted reasonably with semi-analytical modelling.
Speaker: Philippe Vanderbemden (University of Liege) -
46
Hybrid superconducting screens combining disk-shaped bulks and closed-loop coated conductors: modelling and experimental validation
In this communication, we demonstrate numerically and experimentally the remarkable DC magnetic screening ability of hybrid superconducting screens combining a 30 mm-diameter disk-shaped superconducting bulk with different closed superconducting loops made from coated conductors. The loops are placed coaxially with the bulk. The axial, DC and inhomogeneous field to be screened is produced by an air coil. This configuration is studied using a 2D axisymmetric finite element model solved by the H-phi formulation. The measurements are then performed at 77 K using a bespoke, cryogenic 3-axis Hall probe. The results show that such a hybrid superconducting screen allows the maximum shielding factor SF above the bulk to be roughly doubled. In addition, the area of the spatial region for which SF > 2 is multiplied by a factor ~ 4 when compared to a situation involving only a disk-shaped bulk. The finite element model is also used to investigate the influence of the inhomogeneity of the applied field on the screening effect.
Speaker: Nicolas Rotheudt (University of Liège) -
47
A parameter-free reconstruction of HTS critical current magnetic field - angular dependency with sparse measurements
This study delves into the application of sparse sensor placement, a data-driven approach that hinges on identifying an optimal orthogonal basis for representing the angular dependency of high-temperature superconducting tapes and other devices. The proposed method offers the potential to expedite measurements and computations substantially by acquiring data at select locations and reconstructing angular characteristics without needing parameter retrieval or curve fitting to a specific formula. Sparse measurements have shown promise in accurately reconstructing the angular field dependency of critical current, critical current density, and n-value.
Speaker: Dr Paweł Lasek (Silesian University of Technology) -
48
Multi-physics considerations of NI HTS Solenoid for PSI Positron Production Experiment
Please see the attachment for the abstract
Speaker: Jaap Kosse (PSI - Paul Scherrer Institut)
-
45
-
49
Visit PSI labs Paul Scherrer Institute (PSI)
Paul Scherrer Institute (PSI)
-
50
Transfer to Habsburg Castle by bus Paul Scherrer Institute (PSI)
Paul Scherrer Institute (PSI)
-
51
HTS2024 Social Dinner Habsburg Castle
Habsburg Castle
-
52
Transfer to Bad Zurzach by bus
-
18
-
-
Session 3: Applications: B
-
53
Computing Hysteresis and Coupling AC losses in round cable made from filamented HTS tapes
Filamenting is crucial for reducing AC losses in superconducting coated conductor tapes and cables. However, the metallic stabilizing layer can lead to additional energy dissipation due to coupling currents. Estimating AC losses in such cases is challenging due to the complex geometry of the cable. We demonstrate a FEM numerical model suitable for estimation of the AC losses in different configurations of round cables made of filamented tapes, considering both the hysteresis and the coupling losses.
Speaker: Mykola Soloviov (Institute of Electrical Engineering, Slovak Academy of Sciences (SAS)) -
54
Design Optimization of Ferromagnetic Poles for a High Temperature Superconducting Bulk Undulator
This work presents the modelling done to
optimize the pole geometry to be used in the planned high
temperature superconducting bulk undulator in PSI. The H-ϕ
formulation is used to model the undulator field and the
magnetic forces inside the poles. A T-shaped pole with a width
of 10 mm and height of 8 mm was found to be optimal to
maximize the peak undulator field. This model was also used to
generate the data for the shimming algorithm.Speaker: Carlos Gafa (PSI - Paul Scherrer Institut) -
55
Coupled Axial and Transverse Currents Method for Periodic Superconductors Modelling
In this contribution, we present a fast and accurate finite element approach for modelling the electric and magnetic behavior of periodic composite superconducting conductors. It uses two coupled two-dimensional models and accounts for the conductor periodicity via circuit equations. This allows to capture three-dimensional effects while leading to a significant reduction in computational time compared to conventional three-dimensional models. The method is directly applicable to multifilamentary Nb-Ti, Nb$_3$Sn, MgB$_2$, and Bi-2212 wires, and can be extended to other periodic HTS conductor geometries.
Speaker: Julien Dular (CERN) -
56
2D FEM electro-magnetic modelling of straight soldered ReBCO stack cable in high magnetic field
This work presents a 2D FEM modeling approach for a straight soldered ReBCO stack cable within Comsol Multiphysics, focusing on high magnetic field environments. The model incorporates a detailed structure of the ReBCO tapes, including properties like resistivity for the electromagnetic model, as well as the solder shell surrounding the tapes. Critical current dependence on magnetic field strength is derived from experimental data using an interpolation function, enhancing result accuracy. The study reveals specific current sharing patterns between ReBCO tapes within the soldered stack and examines how AC losses vary with external magnetic field direction.
Speaker: Dmitry Sotnikov (PSI - Paul Scherrer Institut)
-
53
-
10:20
Coffee Break & Group Photo
-
Session 3: Applications: C
-
57
Predicting the behavior of insulated REBCO coils up to their operation limit to identify safe operation domain
The development of compact REBCO HTS coils (Rare-EarthBiCaCuO High Temperature Superconductor) with large energy densities face two issues. The first is destructive thermal runaway induced by local dissipative zones, the second is dynamic field homogeneity. The first issue, thermal runaway, may be solved by using a non-insulation or partial insulation technique. These techniques however affect negatively the second issue, as induced current loops may appear both in the tape surface and across coil turns. We observed, as other groups, that an early detection of dissipating voltages makes it possible to discharge isolated coils before a dangerous thermal runaway can occur. However, the dissipating voltage that must be detected is very low, comparable in amplitude to the transient voltage due to magneto-electric effects. Both phenomena must thus be modelled so that their effects can be discriminated in the detection scheme. The combination of both electromagnetic and electro -thermal transient modelling makes it possible to define safe operation scenarios to determine the operation domain of REBCO coils.
Speaker: Dr arnaud badel (Université Grenoble Alpes - CNRS) -
58
High Temperature Superconducting Coating for the Beam Screen of the Future Circular Collider
Abstract—CERN’s next generation particle accelerator, the Future Circular Collider (FCC), aims to reach center-of-mass collision energies of 100 TeV with a 91 km tunnel where charged particles are accelerated and collided. One of the key devices in circular accelerators is the beam screen, responsible for shielding the steering and focusing magnets from the synchrotron radiation generated by the orbiting particles. Due to its proximity to the particle beam, however, it is important that its coupling impedance with the beam is low to avoid the introduction of instabilities. High Temperature Superconductors (HTS) are promising materials for such an application, as they present low surface impedance even at the demanding operating conditions of the FCC, with high magnetic fields of up to 16 T, temperatures of 40-60 K and frequency of 1 GHz. This work evaluates the feasibility of a segmented HTS coating for the FCC beam screen, capable of maintaining high field quality and low surface impedance. Finite Elements Method (FEM) simulations are employed to analyze the electromagnetic and thermomechanical responses of the coated beam screen to regular operation conditions and in the event of a quench of the main dipole magnets.
Keywords— low impedance coating, FEM, HTS, field qualityINTRODUCTION
In circular particle colliders, the particle beam emits synchrotron radiation (SR) due to its circular motion. This radiation poses a threat to the safe operation of the superconducting magnets which, if impinged by it, can surpass their target temperature range. To avoid this, a stainless-steel beam screen (BS) is placed around the particle beam trajectory, absorbing the SR (see Fig. 1) [1]. However, the structure itself interacts with the beam through wake fields and image currents, which can lead to destabilization of the beam orbit. The magnitude of this effect is given by the beam coupling impedance, which depends on the surface impedance and the geometry of the structure surrounding the beam [2]. To minimize it, the beam screen is coated with a highly conductive material. While copper is the standard choice, as is the case with the Large Hadron Collider (LHC), the higher operating temperatures of the BS of the Future Circular Collider (FCC) require a better conductor even at the high magnetic fields targeted by the next generation accelerator.
We acknowledge financial support from PID2021-127297OB-C21, TED2021-130004B-I00 and CEX2019-422 000917-S, FCC-GOV-CC-0208 (KE4947/ATS) and PRTR-C1711 with funds from MICIIN-NGEU-Generalitat de Catalunya. We also thank the Catalan Government for 2021 SGR00440.The employment of rare earth barium copper oxides (REBCO) high temperature superconductors (HTS) has been proposed to achieve this low impedance coating for the FCC BS [3]. Nevertheless, the trapped fields induced by the superconducting magnets in the HTS coating lead to a decrease in the field homogeneity in the vicinity of the beam, which itself represents another source of instabilities. To mitigate this, the coating is split into narrow segments separated by gaps revealing the copper layer below, which decrease the trapped fields and increase field quality in the vacuum chamber, while maintaining low overall surface impedance [4-6]. Beyond these requirements, it is also important to meet thermomechanical requirements both during regular operation and in the event of a magnet quench.
NUMERICAL MODEL
To evaluate the thermomechanical response to the magnetic fields induced by the superconducting magnets in the HTS-coated BS, finite elements method (FEM) analysis was employed, with Multiphysics coupling between electromagnetic, thermal, and mechanical interfaces. All simulations were performed in COMSOL Multiphysics® [7].
The shielding currents induced in the coating by the ramping dipole magnets were calculated through the H-formulation, assuming that there are no currents flowing through any medium other than the HTS [8]. To enforce this, the value of electric resistance used for vacuum and the normal conductors is 1 Ω, and the HTS segments are electronically insulated, that is, the total current flowing through any cross-section is zero [9]. The resistivity of the HTS was defined with Anderson-Kim’s power law with the critical current density J_c and transition index N dependent on temperature, as well as magnetic field intensity and angle, based on material properties of commercially available CCs [10,11]. On a different simulation interface, the image currents induced by the beam in the coating were calculated with the approximation that all materials are perfect conductors, which is the same as restricting all current flow to the very surface of all materials.
To consider the event of a magnet quench, the beam effects were disregarded, and the reduced field formulation was employed to decrease the computational effort required to deal with the quick drop in magnetic field from 16 T to zero. Nevertheless, for the same reason, all materials were considered to have current flow, and therefore their temperature dependent electric resistance values were considered.Fig. 1: Photograph of the beam screen of the Future Circular Collider with interior copper coating. The HTS segments are attached onto the copper coating.
In both scenarios, the heat and force loads were calculated from the electric field, magnetic field and current density obtained from the aforementioned interfaces. A negative heat source with a heat transfer coefficient of 5000 W/(m2K) represents the helium cooling channels located on the top and bottom of the BS. These loads were then used as inputs to calculate the temperature and mechanical stress distributions in the BS with the aid of the solid mechanics and the heat transfer in solids interfaces.
RESULTS
As shown in Fig. 2, the results of the thermomechanical simulations show that there is no expected temperature shift for the regular operation of the HTS-coated BS, when the dipole field is increased at a rate of 0.8 T/min. The heat generated in this case never surpassed 65 mW/m, half of that which would be generated in a full copper coating. With respect to its mechanical response, although the forces are higher than in a full copper coating due to the shielding currents in the HTS, the maximum stress was of 3 MPa, well within the elastic limits of all materials involved, including the HTS coating.
The response to a main dipole magnet quench, however, are quite distinct. Firstly, the high current density induced by the plummeting magnetic field produce up to 30 kW/m, which is enough to bring the maximum temperature to 80 K within the 300 ms of quench. Nevertheless, the temperature stabilized back at 50 K a few seconds after the quench. The force loads also increase to the point of inducing stresses in the range of hundreds of megapascals, but never surpassing the yield stress of the stainless-steel, 1100 MPa, and the stress above which irreversible J_c degradation would occur in the HTS, around 700 MPa.
In terms of both mechanical and thermal behavior, the greatest contribution comes from the copper, where 81% of the heat is generated, as well as 91% of the total forces. This is corroborated by the similarities between these results and the response of a copper-coated BS to a magnet quench, as reported in previous studies [12]. To consider the event of a magnet quench, the beam effects were disregarded, and the reduced field formulation was employed to decrease the computational effort required to deal with the quick drop in magnetic field from 16 T to zero. Nevertheless, for the same reason, all materials were considered to have current flow, and therefore their temperature dependent electric resistance values were considered.Fig. 2: Thermomechanical response of one quadrant of the FCC BS during regular operation and in the event of a magnet quench. Maximum temperatures and mechanical stresses are within the yield stress of stainless-steel and the irreversibility limit of the HTS.
CONCLUSIONS
In this work, we have employed SEM simulation interfaces with COMSOL Multiphysics® to evaluate the response of the HTS-coated FCC BS to the ramping magnetic fields of the main dipole magnets during regular operation and in the event of a magnet quench. We have considered material properties from commercially available CCs to calculate the beam- and magnet-induced currents in the coating as well as their corresponding heat and force loads. The thermomechanical results revealed tolerable temperature shifts and mechanical stresses considering the operating range of the BS and the plastic limit of its materials. Furthermore, since the dominant contributor was the copper already present in the beam screen, the results showed that the performance of the HTS coating with respect to its thermomechanical behavior was comparable to that of a full copper coating.
ACKNOWLEDGMENT
We acknowledge financial support from PID2021-127297OB-C21, TED2021-130004B-I00 and CEX2019-422 000917-S, FCC-GOV-CC-0208 (KE4947/ATS) and PRTR-C1711 with funds from MICIIN-NGEU-Generalitat de Catalunya. We also thank the Catalan Government for 2021 SGR00440.REFERENCES
Abada, A. et al. “FCC Physics Opportunities,” Eur. Phys. J. C 79, 474 (2019).
Calatroni, S., et al. “Thallium-based high-temperature superconductors for beam impedance mitigation in the Future Circular Collider,” Supercond. Sci. Technol. 30, 075002 (2017).
Puig, T. et al. “Coated conductor technology for the beamscreen chamber of future high energy circular colliders,” Supercond. Sci. Technol. 32, 094006 (2019).
Romanov, A. et al. “High frequency response of thick REBCO coated conductors in the framework of the FCC study,” Sci Rep 10, 12325 (2020).
Krkotić, P. et al. “Evaluation of the nonlinear surface resistance of REBCO coated conductors for their use in the FCC-hh beam screen,” Supercond. Sci. Technol. 35 025015 (2022).
Telles, G. T., Romanov, A., Calatroni, S., Granados, X., Puig, T., Gutierrez, J. “Field quality and surface resistance studies of a superconducting REBa2Cu3O7−x—Cu hybrid coating for the FCC beam screen,” Supercond. Sci. Technol. 36, 045001 (2023).
COMSOL Multiphysics® v. 6.2. COMSOL AB, Stockholm, Sweden.
Hong, Z., Coombs, T.A. “Numerical Modelling of AC Loss in Coated Conductors by Finite Element Software Using H Formulation,” J Supercond Nov Magn 23, 1551–1562 (2010).
B. Shen, F. Grilli, T. Coombs, "Overview of H-Formulation: A Versatile Tool for Modeling Electromagnetics in High-Temperature Superconductor Applications," IEEE Access, 8 100403-100414 (2020).
Anderson, P. W., and Kim, Y. B., “Hard Superconductivity: Theory of the Motion of Abrikosov Flux Lines,” Rev. Mod. Phys. 36, 39 (1964).
Wimbush, S., Strickland, N., Pantoja, A., Figshare Dataset (2017).
Bellafont, I. et al. “Design of the future circular hadron collider beam vacuum chamber,” Phys. Rev. Accel. Beams 23, 033201 (2020).Speaker: Guilherme Telles (Institut de Ciència de Materials de Barcelona (ICMAB - CSIC))
-
57
-
59
Summary, awards, conclusion -End of the workshop
-
60
Final Lunch (sandwiches)
-